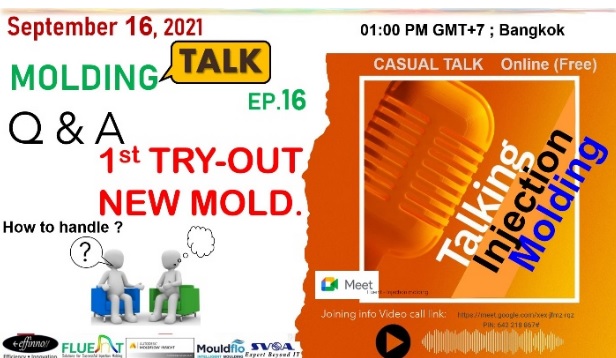
Injection Molding
We launch the 1-hour casual talking every 2 two weeks with Molders after lunch at 1:00 PM through Google Meet. Today, we have Mr. Narongsak (Mr.Jeab), the MD of mold making and molding manufacturer in Nontaburi province (Northen Bangkok area), and two more participants. We regularly have Mr.Hank Tsai from Effinno Technology, Taiwan, as every Molding Talk.
The meeting room opened 30 minutes before the Molding Talk starting time. At 12.45 PM, Mr. Hank was the first one to join. We talked about the story that does not concern 1st Try-out new mold, the subject of today during the wait for the participants.
Hank shared about his new product, which just passed testing with the injection molding process in Taiwan. Hank’s latest product is the digitalized system that helps the Molders control injection molding production to better standardization. The system has been completed in only the Chinese language, and the English version will finish in October as planned. At about 1.05 PM, the participants joined us; the 1st try-out new mold started.
1st try-out new mold today we agreed to talk with three categories related to the subject—1st Preparation for the try-out, 2nd Implementation and 3rd the Result analysis.
Preparation for the 1st Try-out new mold, Hank and Narongsak, and I agreed that before installing the mold to the machine, we need to ” Compare checking the real mold with the Mold design drawing.”
The Correct CAE Simulation(Moldflow) result or report is the second one is an essential thing we should pay attention to before starting the 1 st shot. The simulation results can give us the “Molding processing window” to help the molders set up the injection conditions for the first shot without trial and error; fill speed range, melt temperature, injection pressure setting, packing/holding pressure, cooling time. What Hank mentioned about simulation is the key to success if we talk about CAE Simulation. The key to success is to “Link” the simulation results to the injection molding machine effectively.
Mac from Fluent – Injection molding shared his idea about CAE simulation when using simulation results with the 1st try-out. The simulation results should be done by a qualified engineer and reliable. Suggest working with the simulation engineer who has a guarantee from the OEM simulation software. The simulation work has often been done since the beginning of the mold design and mold making, but the mold design is different from the simulation. Imagine! If you have the perfect simulation results, which already gave and guided for the optimum mold design. But, the mold designer did not use that for reference and designed the mold with different ideas, resulting in the worst situation. The CAE simulation is useless, Mac said.
It’s 2 O’clock already. We have to stop today Molding Talk. Mac proposes extending more 10-15 minutes because he can catch a great idea from HANK and Narongsak and want to talk more about that. The ” Objective” of 1st try-out new mold is what’s Mac can catch from 2 senior molders. The objective to robust the molding cycle consistency is the explanation from HANK. The cushion result from the continuous cycle can tell us the process consistency and can be robust the molding process, Narongak said. I can say “Yes” I have fully agreed with both of them, but time is up for today’s Molding Talk.
We will continue to talk again to clarify the “Objective” of 1st Try-out new mold in Molding Talk next two weeks.
The past episode, EP.1 – EP.16 were recorded by Google Meet video recording system. Follow this link https://tinyurl.com/h544xnbv if you interest in checking out our Molding Talk recorded?
Molding Talk EP.17 will be back to meet you again on September 30, 2021. at 1:00 PM ( Bangkok).
For more information, please visit www.fluent.co.th
To Subscribe to Molding Talk News, hit his below link. http://eepurl.com/g01BWn