การปรับปรุงประสิทธิภาพการหล่อเย็น
ในแม่พิมพ์ฉีดพลาสติกที่ออกแบบและสร้าง ควรมีคู่มือการต่อวงจรของการหล่อเย็น หรือ ไดอะแกรมแนะนำการต่อพ่วงระบบหล่อเย็นที่กำหนดโดยวิศวกรออกแบบ เชื่อว่าทุกท่านเห็นด้วยกับเรื่องนี้ ครั้งหนึ่งในการทำงานกับแม่พิมพ์ใหม่ร่วมกับเพื่อนร่วมงานใหม่ การหล่อเย็นแม่พิมพ์ และการวัดค่าได้เป็นสิ่งที่พวกเขาให้ความสำคัญมาก ทุกๆ แม่พิมพ์จะระบุอัตราการไหลของน้ำที่ต้องการมีหน่วยเป็นแกลลอนต่อนาที (GPM) ไว้ที่บนแผ่นวงจรที่ติดอยู่กับแม่พิมพ์ ใช้กล่องควบคุมน้ำ (Manifold) ที่มีเซ็นเซอร์ดิจิตอลวัดอัตราการไหลและวัดอุณหภูมิ ที่ทางออกและทางเข้ากล่องควบคุมน้ำ ถัดมาใกล้ๆกัน บนชุดควบคุมน้ำมีวาล์วที่ควบคุมการเปิดปิดน้ำที่ควบคุมการไหลของน้ำได้ด้วยมือและแยกเฉพาะสำหรับวงจรน้ำแต่ละวงจรที่จะเข้าสู่แม่พิมพ์ ทุกๆช่องทางน้ำไหลมีการกำหนดสีฟ้า และ สีแดงเป็นการควบคุมด้วยสายตา (Visual Control) และระบุตำแหน่งของท่อพ่วง(HOSE) อย่างชัดเจน แม่พิมพ์ทุกแม่พิมพ์ มีการออกแบบและสร้างตามคู่มือมาตรฐานแม่พิมพ์ (Mold making standard) การทดลองแม่พิมพ์และการประเมินผลจากการทดลองผลิตจริง(Validation and Pilot) ใช้หลักทางวิทยาศาสตร์ (Scientific Molding) และมีรายงานผลการทดลองที่มีข้อมูลที่น่าเชื่อถือ ก่อนการส่งมอบแม่พิมพ์ใหม่แก่ลูกค้ามีการตรวจสอบ และ ประเมินตามวิธีการตรวจสอบแม่พิมพ์และอนุมัติแม่พิมพ์ (Mold Evaluation and Commissioning) มีขั้นตอนหนึ่งที่เมื่อแม่พิมพ์ใหม่เสร็จ จะทดสอบการไหลของน้ำในแม่พิมพ์และรายงานผลอัตราการไหลของแต่ละวงจรแยกอิสระกัน โดยมีปั๊มที่ปรับค่าได้เป็นตัวกำหนดแรงดันและอัตราการไหลเพื่อส่งเข้าสู่แม่พิมพ์ในแต่ละวงจร เป็นการจำลองการไหลด้วยอัตราการไหลในสภาวะการผลิต รายงานผล อัตราการไหล และ Reynolds number เปรียบเทียบกับการออกแบบการหล่อเย็นด้วย Moldflow Simulation ภายใต้ค่าความดันและ อัตราการไหลของน้ำที่กำหนด ก่อนส่งมอบแม่พิมพ์พร้อมรายงาน
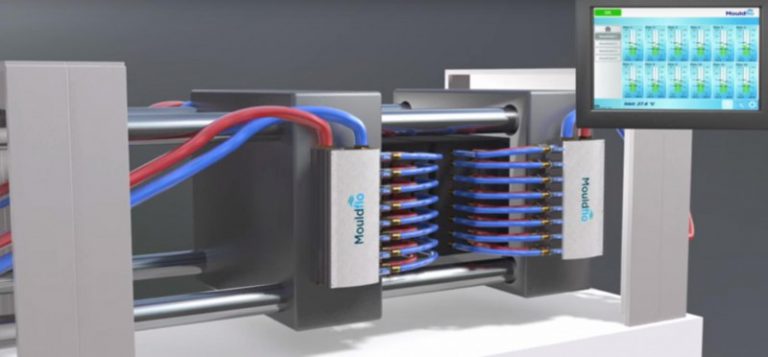
1. เวลาหล่อเย็นและอัตราการลดลงของอุณหภูมิพลาสติกเหลวในแม่พิมพ์
เวลาหล่อเย็น เป็นช่วงเวลาที่นานที่สุดใน 1 ไซเคิลของกระบวนการฉีดพลาสติก 70% ของ ไซเคิลไทม์ เป็น เวลาของเวลาหล่อเย็น(Cooling time) นอกจากเวลานานแล้ว สิ่งที่เวลาหล่อเย็นมีผลกระทบมากและวิกฤต คือ ขนาด หรือ Dimension ของชิ้นงาน การที่จะควบคุมกระบวนการให้เสฐียร มีของเสียในอัตราที่กำหนด (%Yield) เช่น ครั้งหนึ่งเมื่อมีเป้าหมาย %Yield 98% ในการผลิตชิ้นงานด้วย พลาสติก PPS 40GF 8 คาวิตี้ x 2 โอเวอร์โมลดิ้ง PPS เป็นพลาสติกที่ต้องขึ้นรูปภายใต้อุณหภูมิแม่พิมพ์ที่สูงถึง 150 องศาเซลเซียส และ อุณหภูมิหัวฉีด 320 องศาเซลเซียส อุณหภูมิโก่งตัว (HDT หรือ HDTUL) 220 องศาเซลเซียส PPS เป็นพลาสติกแบบมีผลึกเป็นสัญฐาน มีความแข็งแกร่ง ทนต่อความร้อนสูงได้และทนทานต่อสารเคมี คงขนาดและรักษาสมบัติได้ดีมากแม้อุณหภูมิมีการเปลียนแปลงแบบฉับพลัน ด้วยเป้าหมายการผลิต 24 ชั่วโมง เพื่อให้ได้เอ้าท์พุทตามที่กำหนด อัตราการแลกเปลี่ยนความร้อนในแต่ละไซเคิลไทม์ควรสม่ำเสมอ และ คงที่ ในทุกๆ รอบ การลดลงของอุณภูมิพลาสติกภายในแม่พิมพ์ใช้เวลาเพียงสั้นๆ ภายใต้อุณหภูมิแม่พิมพ์สูงถึง 150 องศาเซลเซียส ดังนั้น ในการการออกแบบแม่พิมพ์และคำนวณเวลาหล่อเย็น อาจต้องคำนึงถึงความร้อนจำเพาะและความสามารถในการนำความร้อนของวัสดุแม่พิมพ์ (Mold specific Heat / Mold Thermal Conductivity) วิธีในการทดลองและอนุมัติแม่พิมพ์ ระยะเวลาในการประเมินแม่พิมพ์ วิธีการเก็บตัวอย่าง การตรวจสอบคุณภาพ การกำหนดหน้าต่างกระบวนการ เพื่อไม่ให้ต้องกำหนดเวลาหล่อเย็นให้ยาวนานกว่าที่ควรจะเป็น วิธีการทดลองแม่พิมพ์ด้วยระยะเวลาสั้นๆ จำนวนไซเคิลในการทดลองเพียงไม่มากพอ ข้อมูลจากการทดลองที่มาสมบูรณ์มากพอไม่อาจเป็นตัวแทนในการทำงานของแม่พิมพ์ในสภาวะการผลิตได้
2. การวัดค่าอัตราการไหล และอุณหภูมิของน้ำ การกำหนดค่า Reynolds Number และควบคุมแบบเรียลไทม์
ในขณะการฉีดพลาสติก เราจำเป็นต้องนำความร้อนออกจากแม่พิมพ์ เนื่องจากทุกๆไซเคิลมีการนำเข้าความร้อนจากพลาสติกเหลวซึ่งมีอุณหภูมิสุงกว่าเหล็กแม่พิมพ์ การแลกเปลี่ยนความร้อนในโมลด์ เกิดขึ้นระหว่าง 2 วัตถุ คือ การถ่ายเทจากพลาสติกเหลวสู่เหล็กแม่พิมพ์ และ จากเหล็กแม่พิมพ์สู่น้ำหล่อเย็นที่ไหลผ่าน ผลต่าง ΔT ของอุณหภูมิระหว่าง 2 วัตถุ ทำให้เกิดการหดตัวของชิ้นงานพลาสติกทันทีที่สัมผัสจนกระทั่งก่อนที่จะฉีดย้ำ การหดตัวของพลาสติกในแม่พิมพ์จะเกิดการหดตัวมากในแนวความหนาของชิ้นงาน การหดตัวจะทำให้พื้นผิวของชิ้นงานผละออกมาจากผิวแม่พิมพ์ และหากพิจารณาให้ดีแล้วการถ่ายเทความร้อนเกิดที่ผิวสัมผัสระหว่างชิ้นงานพลาสติกและผิวแม่พิมพ์ หากผิวไม่เกิดการสัมผัสอย่างสมบูรณ์ (ที่มา : Plastic technology) หรือ ชิ้นงานเกิดการหดตัวมาก ผละออกจากผิวแม่พิมพ์ ผิวสัมผัสจะน้อยลง ดังนั้น การถ่ายเทความร้อนออกจากชิ้นงานพลาสติกสู่เหล็กแม่พิมพ์ก็จะแย่ลงด้วย การใช้ความดันย้ำและการฉีดย้ำที่เหมาะสมจะทำให้การถ่ายเทความร้อนดีขึ้นเนื่องจากผิวชิ้นงานสัมผัสกับผิวแม่พิมพ์ ΔT, ระหว่างเหล็กแม่พิมพ์และน้ำหล่อเย็นมีความแตกต่างกันมากเช่นกัน แต่มีความซับซ้อนกว่าการทำความเข้าใจ สามารถคำนวณหาอัตราการถ่ายเทความร้อนได้ จากค่า Reynolds Number , Heat transfer coefficient และ Heat Flow rate ที่จะสามารถอธิบายถึงการถ่ายเทความร้อนของการไหลของของไหลในท่อว่าเป็นอย่างไร การเข้าใจพฤติกรรมการไหลสามารถช่วยให้กำหนดความสามารถสูงสุดของการถ่ายเทความร้อนได้ ถ้าน้ำไหลในอัตราการไหลที่ช้ามากภายในท่อ การไหลรูปแบบนี้จะเรียกว่าการไหลแบบราบเรียบ (Laminar) ซึ่งลักษณะเช่นนี้จะทำให้บริเวณผนังของท่อมีการถ่ายเทความร้อนต่ำ และน้ำจะร้อนขึ้น และหากการไหลในท่อเร็วขึ้น และเป็นการไหลแบบปั่นป่วน(Turbulence) การถ่ายเทความร้อนก็จะมีประสิทธิภาพดีขึ้น ในการควบคุมกระบวนการผลิตโดยที่การฉีดพลาสติกสามารถควบคุมและชี้วัดได้ถึงอัตราการไหลและความแตกต่างระหว่างอุณหภูมิที่ทางน้ำเข้าและทางน้ำออกได้ และสามารถปรับเปลี่ยนอัตราการไหลของน้ำในแม่พิมพ์ได้เพื่อให้การไหลของน้ำหล่อเย็นในแม่พิมพ์ของทุกๆ วงจรการไหลของน้ำอยู่ในค่าที่เหมาะสมตลอดระยะเวลาการผลิต สามารถมอนิเตอร์ข้อมูลต่างๆ ดังกล่าวได้ผ่านหน้าจอของเครื่องฉีดพลาสติกหรือ หน้าจอแสดงผลจากเครื่องมือการวัด มีเครื่องมือแสนฉลาดในเครื่องฉีดพลาสติก ที่ออกแบบโมดูลแบบวงจรปิดและฉลาดที่จะปรับค่าเองโดยอัตโนมัติ (Automatic Close-loop Cooling monitoring) ผลดีคือการไหลของน้ำในแม่พิมพได้รับการกำหนดค่าที่เหมาะสมตั้งแต่เริ่มต้น และ มีการมอนิเตอร์ และ ควบคุมแบบอัตโนมัติให้ค่าอัตราการไหล, ความดัน และอุณหภูมิอยู่ในค่าที่ต้องการเสมอ (รูปที่ 3 (a)) หรือ การออกแบบเครื่องมือแสนฉลาดในการช่วยวัดค่าอัตราการไหล, ความดัน และอุณหภูมิ ของระบบหล่อเย็นในแม่พิมพ์ฉีดพลาสติกให้อยู่ในค่าที่ต้องการเสมอเช่นกัน ส่งข้อความ รายงานผ่านอีเมล์ มือถือและแทปเลตแบบเรียลไทม์ (รูปที่ 3 (b))
3. พลังงานความร้อนในแม่พิมพ์ การหลอมเหลวของพลาสติก พลังงานอินพุท และ การหล่อเย็น
เมื่อออกแบบแม่พิมพ์ ควรคำนวณเสมอ ว่าขนาดท่อน้ำควรโตเท่าไร สำหรับแม่พิมพ์ที่มีขนาดและความยาวของช่องทางไหลของน้ำที่แตกต่างกัน เป้าหมายคืออัตราการไหลเข้า – ออก และ Reynolds number ที่เหมาะสมต่อการพาความร้อนออกภายใต้สภาวะการไหลแบบปั่นป่วน (Turbulence) พลังงานความร้อนที่ต้องพาออกไป และไซเคิลไทม์ ที่กำหนด การถ่ายเทความร้อนแปรผันโดยตรงกับ Reynolds number การไหลแบบปั่นป่วน จะเกิดเมื่อ Reynold’s number มีค่ามากกว่า 3,500 ขึ้นไป (ในทางปฏิบัติผมมักใช้ค่า 4,000) ค่าพลังงานความร้อนขึ้นกับกลไกการเปลี่ยนแปลงสภาวะของพลาสติก ซึ่งคือการเปลี่ยนแปลงสภาวะทางความร้อน ได้แก่ อุณหภูมิการเปลี่ยนสภาวะ ; Tg(Glass Transition Temperature) Tg พบทั้งในพลาสติกมีผลึกและไม่มีผลึก และอุณหภูมิจุดหลอมเหลว Tm; (Melting point Temperature) และ อุณหภูมิการขึ้นรูป Nozzle temperature
แนวคิดของการปรับปรุงหรือออกแบบระบบหล่อเย็นคือการออกแบบขนาดความโตท่อน้ำ ความยาวของท่อน้ำที่เหมาะสม และมีอุณหภูมิของน้ำที่ทางออกเพิ่มขึ้นไม่เกินค่า ∆T ที่กำหนด เพื่อให้การไหลของน้ำในท่อสามารถพาเอาพลังงานความร้อนจากพลาสติกเหลวที่ไหลเข้าสู่แม่พิมพ์ในทุกๆ ไซเคิลออกในอัตราที่กำหนด
Polymer thermalproperties
เริ่มต้นจาก Polymer thermal properties ของพลาสติกที่ไม่มีผลึกและพลาสติกที่มีผลึก กลไกการเปลี่ยนสภาพจากของแข็งเป็นพลาสติกเหลวแตกต่างกัน ในตำราภาษาอังกฤษที่อธิบายถึงพอลิเมอร์และพลังงานมักเป็นตำราจากประเทศสหรัฐอเมริกา เราจะพบหน่วยของพลังงานจากตำราเหล่านั้นเป็นหน่วย BTU (British Thermal Unit) ความหมายของ 1 BTU หมายถึง พลังงานที่ต้องการที่จะทำให้น้ำ ที่มีน้ำหนัก 1 ปอนด์ (lb.) มีอุณหภูมิเพิ่มขึ้น 1 ° F ค่าพลังงานนี้ เรียกว่าค่าความจุความร้อน(heat capacity มีอักษรย่อ CP). วัสดุต่างๆ มีค่า Cp ของตัวเอง สามารถคำนวณหาค่าพลังงานได้จากความสัมพันธ์
E = W x CP x ∆T หน่วย BTU ; W = น้ำหนักของวัสดุหน่วย ปอนด์ ; lb
CP = Heat Capacity in BTU/(lb*°F),
∆T = อุณหภูมิที่เปลี่ยนแปลง, °F.
ในการฉีดพลาสติกสามารถทำความเข้าใจได้ว่า พลังงานที่ใช้ในการทำให้พลาสติกเปลี่ยนจากของแข็งไปเป็นพลาสติกเหลวมีค่าพลังงานเท่ากับพลังงานที่เปลี่ยนสภาวะจากของเหลวให้เป็นของแข็งอีกครั้ง เช่น ชิ้นงานพลาสติก ABS และรันเนอร์น้ำหนักรวม 0.45 lb หากต้องฉีดขึ้นรูปต้องหลอมเหลว ABS ที่ 464 °F และปล่อยให้เย็นตัวลงมาที่ 212 °F จากนั้นจึงกระทุ้งออกจากแม่พิมพ์โดยชิ้นงานไม่เสียรูป จากตารางที่ 2 heat capacity of ABS เท่ากับ 0.34 BTU/(lb*°F) คำนวณพลังงาน ในที่นี้คือ ตัวอักษร E ที่ต้องการได้ จาก
E = 0.45 lb x 0.34 BTU/(lb*°F) x (464-212) °F = 0.45 x 0.34 x 252 = 38.56 BTU
พลังงาน 38.56 BTU คือพลังงานที่ต้องการเพื่อทำให้หลอมเหลวที่ 464 °F และทำให้กลับไปสู่สภาวะของแข็งอีกครั้งที่ 212 °F. เรียกพลังงานนี้ว่า Cooling energy สำหรับ 1 shot.
4. อัตราพลังงานความร้อนที่เข้าสู่แม่พิมพ์ เท่ากับ อัตราการพาพลังงานความร้อนออก (Cooling energy Flow Rate)
อัตราการนำเข้าและนำออก หรือ เรียกว่า Cooling energy Flow Rate ( Q ) พิจารณาจากไซเคิลไทม์ในการฉีดพลาสติกเหลวเข้าสู่แม่พิมพ์ ทำได้ไม่ยาก โดยคำนวณหาจำนวน shot ต่อ 1 ชั่วโมง (Shot per Hour ; SPH)และ Cooling energy Flow Rate จากค่าพลังงานต่อ 1 shot ใน (3) เช่น หาก 1 ไซเคิล = 15 วินาที
SPH = 3600/15 = 240 shots/hour. (Cooling energy = 38.56BTU/shot)
Q = SPH x BTU/shot = 240 x 38.56 = 9254.4 BTU/hour;
ตารางที่ 1 : Heat Capacity of common Polymer ; ที่มา : smartflow-usa.com
|
Morphology |
Cp ; Heat Capacity, BTU/(lb*°F) |
Crystallization Heat of Fusion, BTU / (ib*°F) [Latent Heat] |
Nozzle Temperature, °F / °C |
Ejection Temperature, °F / °C |
ABS |
Amorphous |
0.34 |
0.0 |
464 |
212 |
PS |
Amorphous |
0.43 |
0.0 |
475 |
203 |
PMMA |
Amorphous |
0.46 |
0.0 |
464 |
185 |
PC |
Amorphous |
0.38 |
0.0 |
554 |
284 |
PP |
Crystalline |
0.61 |
89.1 |
450 |
212 |
HDPE |
Crystalline |
0.56 |
119.8 |
450 |
212 |
LDPE |
Crystalline |
0.62 |
56.0 |
446 |
194 |
POM |
Crystalline |
0.43 |
60.0 |
430 |
284 |
PA6 |
Crystalline |
0.61 |
89.1 |
450 |
212 |
พลาสติกกึ่งผลึก (Semi – Crystalline) มีการคำนวณพลังงานเหมือนกับพอลิเมอร์อสัญฐาน(Amorphous) เพียงแต่จะต้องคำนึงถึงค่าพลังงานพิเศษที่ต้องใช้เพิ่มเข้ามาในขั้นตอนการหลอมผลึก เนื่องจากพอลีเมอร์กึ่งผลึกมีความแข็งแรง ทนต่อความร้อน โมเลกุลมีการจัดเรียงตัวอย่างเป็นระเบียบ ผลึกที่เกิดขึ้นมีตั้งแต่ 10% – 80% พลังงานในการหลอมผลึกนี้ เรียกว่า Latent Heat . โมเลกุลผลึกจะออกจากกันและเกิดการหลอมกลายเป็นโครงสร้างอสัณฐานก่อนจากนั้นถึงจุดหลอมเหลว (Melting point)
การคำนวณพลังงาน จะต้องรวมเอาค่าพลังงานในส่วนของ Latent Heat เข้าไปด้วย ยกตัวอย่างการคำนวณพลังงาน Cooling energy ของ PP; Poly(propylene) ที่มีน้ำหนักต่อ Shot 0.30 lb.( 136 กรัม) ไซเคิลไทม์ 8 วินาที
จากตารางที่ 2 CP = 0.61 BTU/(lb*°F), ∆T (450-212 = 238), latent heat value (HL) = 89.1 BTU/lb.
คำนวณพลังงานที่จะหลอมเหลวพลาสติก PP
E/shot = W x ((CP x ∆T) + HL)
E/shot = 0.30 x ((0.61 x 238) + 89.1) = 0.30 x (145.2 + 89.1) = 0.30 x 234.3 = 70.3 BTU/shot.
เช่นเดียวกัน Cooling energy Flow Rate ต่อชั่วโมง SPH=3600/8 = 450shots. ค่าอัตราพลังงานหล่อเย็นต่อ 1 ชั่วโมง คำนวณจาก 450 shots
Q=70.3 BTU/shot x 450 SPH = 31,635 BTU/hr.
ต่อไป มาถึงจุดสำคัญที่สุดที่จะต้องออกแบบแม่พิมพ์ เพื่อหล่อเย็น ABS ให้เกิดการพาพลังงานออกจากแม่พิมพ์ 9,254.4 BTU/hour หรือ การหล่อเย็น PP เพื่อพาพลังงานออก 31,635 BTU/hr.
ฟังก์ชันหลักของแม่พิมพ์ฉีดพลาสติกคือการแลกเปลี่ยนความร้อน ความร้อนอินพุทคือพลาสติกหลอมเหลวที่ฉีดเข้าไปในแม่พิมพ์ด้วยอัตราพลังงานต่อ 1 ชั่วโมง ( Cooling energy Flow Rate ; Q) การนำพาความร้อนออกจากแม่พิมพ์จะต้องมีอัตราการหล่อเย็นที่เพียงพอเพื่อให้เกิดการเย็นตัวลงสู่อุณหภูมิกระทุ้งชิ้นงาน และเพื่อรักษาอุณหภูมิของแม่พิมพ์ให้คงที่เหมาะสมสำหรับการผลิต
5. การออกแบบหรือตรวจสอบขนาดความโตของท่อน้ำ และ ความยาวของท่อน้ำ Reynolds number, Heat Transfer Coefficient และ Heat Flow Rate
ท่อน้ำที่มีขนาดเล็กมักเกิดการสูญเสียความดันขณะไหลและมีการสะสมความร้อน มีอุณหภูมิน้ำขาออกสูงขึ้น เนื่องจากมีอัตราการไหลต่ำ ในขณะเดียวกันการพาความร้อนในท่อน้ำที่มีขนาดใหญ่กว่ามีอัตราการไหลที่ดีกว่า เริ่มจากการออกแบบขนาดความโตของท่อน้ำหล่อเย็น วิศวกรสามารถตรวจสอบความเหมาะสมในการเกิดการไหลแบบปั่นป่วนได้จากการคำนวณหาค่า Reynolds number (Re)≥ 4,000
Reynolds number; Re สามารถคำนวณหาได้จากสมการของ Oswald Reynolds*
Re = [3160 x Q ] ÷ [D x n] ; Re = Reynolds number
Q = จำนวนแกลลอน ต่อ นาที ; GPM)
D = เส้นผ่านศูนย์กลางของท่อน้ำ (นิ้ว)
n = kinematic viscosity, centistokes (cs),
*http://www.engineersedge.com/fluid_flow/kinematic-viscosity-table.htm
Heat transfer Coefficient และ Heat Flow Rate เป็นความสัมพันธ์ของค่าความนำความร้อนของของเหลวที่ใช้ในแม่พิมพ์ พื้นที่ผิวที่ของเหลวสามารถพาความร้อนออกไปได้สัมพันธ์โดยตรงกับขนาดความโตของท่อ นอกจากนี้ยังมีความสำพันธ์กับ Reynolds number และความแตกต่างของอุณหภูมิของแม่พิมพ์และอุณหภูมิของของเหลว การคำนวณ Heat transfer coefficient เป็นขั้นตอนการคำนวณเพื่อที่จะคำนวณหา Heat Flow Rate(Q ; BTU/Hour) ในขั้นตอนสุดท้าย ทำการแปรผันค่าความโตท่อ และความยาวท่อเพื่อคำนวณและพิจารณาผลลัพธ์ที่ Heat Flow Rate สามารถครอบคลุมค่า Cooling energy Flow Rate (จาก 4. )
ตารางที่ 3 ในการออกแบบเริ่มต้น ชิ้นงานเป็นพลาสติกแบบมีผลึก น้ำหนัก 0.5 ปอนด์ ต่อ 1 shot กำหนดให้ท่อน้ำมีขนาดเส้นผ่านศูนย์กลาง 0.6 นิ้ว หรือ ประมาณ 15 mm ในการตรวจสอบการไหลของน้ำหล่อเย็น พบว่าเป็นการไหลแบบปั่นป่วน โดยมี Reynolds number เท่ากับ 7,104.11 พลังงานในการหลอมเหลวพลาสติก PP ให้หลอมเหลวต้องใช้ Cooling energy Flow Rate38,230.20BTU/Hour หรืออีกนัยหนึ่งคือ ในการที่จะทำให้พลาสติกเย็นตัวลงก็ต้องพาความร้อนออกไปในปริมาณเท่าๆ กัน เพื่อให้เกิดการพาความร้อนออกจากแม่พิมพ์ จำเป็นต้องมีจำนวณท่อน้ำถึง 4 ท่อ เพื่อให้เกิด Heat Flow Rate มากเพียงพอ
6. ตรวจสอบ การออกแบบระบบหล่อเย็นในขั้นตอน Design Review อย่างรอบคอบ
ผลการออกแบบการหล่อเย็นแม่พิมพ์ วิศวกรสามารถตรวจสอบได้ด้วย Moldflow Cooling Design ก่อนที่จะมีการอนุมัติให้ผลิตแม่พิมพ์ ผลลัพธ์สำคัญต่างๆ เช่น Mold temperature, Circuit Coolant temperature, Frozen layer Part (at end of Fill) เพื่อพิจารณาถึงความสามารถในการฉีดย้ำ (Filling + Holding pressure), Time to reach ejection temperature เป็นต้น การกำหนดการตรวจสอบการออกแบบระบบหล่อเย็นให้เป็นมาตรฐานการตรวจสอบขั้นตอนหนึ่งในการรีวิวการออกแบบ โดยไม่ลืมที่จะระบุข้อมูลในรายงานการออกแบบแม่พิมพ์เพื่อการผลิตในทุกๆครั้ง (Mold Design For manufacturing; DFM)
เพื่อ กระบวนการฉีดพลาสติกที่เสฐียร จำเป็นต้องมีแม่พิมพ์ที่เสฐียร เครื่องฉีดพลาสติกที่อยู่ในสภาพดี การหล่อเย็นมีอัตราการไหลของน้ำหล่อเย็นที่สม่ำเสมอในแต่ละรอบการทำงาน การแลกเปลี่ยนความร้อนจะต้องคงที่ หากต้องการชิ้นงานที่มีความเสฐียรในคุณภาพ กระบวนการถ่ายเทความร้อนควรจะสฐียรแบบไซเคิลต่อไซเคิล และ ล้อตต่อล้อตของการผลิต แม่พิมพ์จะต้องสามารถรักษาอัตราการไหลเพื่อให้เกิดการไหลแบบปั่นป่วน อุณภูมิน้ำออกไม่เพิ่มขึ้นสูง ได้ตามเกณฑ์ที่กำหนดอัคราการไหลของน้ำหล่อเย็น ไม่เกิดความดันสูญเสียในการไหล ไม่เกิดจุดหยุดชะงักและสะสมความร้อน เราสามารถออกแบบและตรวจสอบผลการออกแบบระบบหล่อเย็นได้จากการคำนวณค่าพลังงานความร้อน ขนาดท่อ ความยาวท่อจากแบบที่กำลังรีวิวก่อนอนุญาตให้ตัดเฉือน แม่พิมพ์ใหม่ควรทดสอบด้วยเครื่องมือ วัดค่า บันทึก และรายงานผล ในกระบวนการผลิตแบบแมสโปรดักชั่น การกำหนดค่าอัตราการไหล การควบคุมค่าอุณหภูมิน้ำขาออกให้อยู่ในค่าที่กำหนด และมอนิเตอร์อยู่ตลอด เป็นการควบคุมกระบวนการที่ดีและช่วยให้กระบวนการผลิตมีความเป็นมาตรฐานและเป็นระบบมากขึ้น นอกจากนี้ การออกแบบระบบการซ่อมบำรุงแม่พิมพ์เชิงป้องกัน ร่วมกับการตรวจสอบและปรับปรุงระบบการไหลเวียนของน้ำทั้งระบบของโรงงานอย่างสม่ำเสมอ ทั้งหมดจะต้องทำไปพร้อมๆ กัน การเก็บข้อมูลที่ดี คนทำงาน วิศวกร ผู้บริหารต่างสามารถใช้ข้อมูลในการปรับปรุงกระบวนการและประกอบการระบุสาเหตุของปัญหาและการตัดสินใจได้อย่างถูกต้อง.
– ขอบคุณSvoa Public Co. Ltd. และ AUTODESK THAILAND ที่เอื้อเฟื้อ Software Autodesk Moldflow Insight Ultimate 2018.R2